表面处理技术、工艺类型和方法
有多种表面精加工技术和方法来精加工零件,每种方法都会产生不同的表面光洁度和平整度。
研磨工艺
研磨是一种精密操作,基于载体中的研磨料游离磨粒或复合研磨盘基质中的固定磨粒的切割能力。有两种类型的研磨工艺: 金刚石或传统磨料。只要控制和监测研磨盘的平整度,任何一种研磨工艺都可以产生低至 0.0003 毫米的平整度结果。研磨过程是一种温和的切削过程,它将研磨盘的平整度转移到被研磨的部件上,而不会对部件施加任何应力,因为整个表面都是同时加工的。这与典型的 CNC、车削、铣削和磨削工艺不同,在这些工艺中,切割始终集中在特定区域。尽管任何研磨工艺都能够产生平整度,但金刚石和复合盘的工艺组合可实现更广泛的表面光洁度。
抛光工艺
抛光通常在研磨操作后进行,以达到最终的表面光洁度。抛光的一些主要因素是:达到镜面,改善外观,达到最佳密封面,光学测量平整度,改善电接触,提高材料的光学质量
化学机械抛光(CMP)
化学机械抛光或平面化学抛光是利用化学和机械力的结合来平滑表面的过程。它可以被认为是化学蚀刻和自由研磨抛光(研磨)的混合体。当需要非常低的 Ra 或需要无划痕的显微图像时,CMP 工艺很常见,例如用于显微硬度测试的冶金样品。
干式电解抛光
干式电解抛光可保留铸件或机加工部件的几何形状且不会使边缘变圆角,它可以去除打磨图案以提供明亮的镜面饰面。也能够处理复杂的几何形状,而不会在表面留下微划痕,同时保持组件公差。它比液体电解抛光更有效,液体电解抛光通常仅将表面粗糙度降低 50%。
离心式抛光
离心式抛光产生非常高的重力,驱动机构设计为产生比正常重力高 5-25 倍的高“G”力,3 或 4 个六边形/圆形桶安装在转塔上。转塔和机筒沿相反方向高速旋转,由此产生的离心力增加了机筒中磨料介质的重量,磨料介质与部件(也在机筒中)滑动,以产生快速切割动作
磨削工艺
磨削是一种使用较粗磨料的加工工艺。
振动精磨工艺
振动精加工是一种大规模精加工工艺,用于使用特殊形状的介质颗粒对大量相对较小的工件进行去毛刺、倒圆角、去氧化皮、抛光、清洁和光亮处理
拖动精加工
拖曳精加工是振动精加工的特殊版本。不同之处在于,待去毛刺和精加工的零件在连接到固定装置时通过介质机械拖动。这可以防止部件相互接触。
表面处理标准
有多种表面处理标准,到目前为此最常见的是 Ra 和 Rz。 Ra 是给定样品长度上的粗糙度平均值,虽然很常见,但由于它是平均值,它确实有可能遗漏可能不符合 Ra 目标精神的显着划痕。 Rz 标准为过程提供了更好的整体粗糙度数据,首先将样本长度分成较小的扇区,然后对每个扇区进行最坏情况的峰谷测量,然后显示较小扇区组合值的平均值。表面处理标准本身就是一个详细的主题。
算术平均粗糙度值 RA
粗糙度轮廓的总高度 Rt、平均粗糙度深度 Rz 和最大粗糙度深度 Rz1max
平均槽间距 RSm 是型材元素间距 Xsi 的平均值
型材的材料成分曲线描绘了型材的材料成分 Rmr(c) 作为截面高度 c(Abbott-Firestone Curve) 的函数
为什么表面处理很重要
由于许多不同的原因,需要定义组件的表面光洁度。最基本的是美学,但表面光洁度也可以控制部分的磨损特性,表面保持润滑的能力两个硬面产生良好的密封和许多其他重要目标都取决于生成的表面光洁度。工程图上的表面光洁度用勾号表示。这个符号表示所需的平整度
以下是技术图纸的摘录,其中显示了所需表面光洁度的示例
技术图纸上表面光洁度的典型说明:
符号 A 如何指定以 Ra 微米为单位的最大粗糙度值。
符号 B 如何指定最大和最小粗糙度值。
符号 C 如何指定最大粗糙度和精加工工艺。
如何测量表面光洁度
有两种测量表面光洁度的方法。接触式和非接触式测量系统。接触系统使用红宝石球或金刚石触针,考虑到表面上的波峰和波谷,它们以单一的短迹线穿过零件的表面。然后使用复杂的算法和公式将其转换为表面光洁度数字。这是成本较低的方法,简单的手持工具价格合理。使用干涉仪等非接触式系统时,激光会从表面反射,从而提供表面的 三维渲染。这是一种更昂贵的解决方案,但确实考虑了被测量的整个表面,而不仅仅是单个迹线。这种类型的测量系统对于光学表面光洁度测量更为重要。对于大多数工程应用,接触系统是可以接受的。
相关表面处理技术案例研究
典型的表面处理问题及解决方法
橘皮
假设您的工件中没有任何线条,并且表面光洁度很高,但是看起来像是镀铬橙色的表面。这种橘皮现象几乎总是由抛光过程中对钢材施加过大的应力,即过度抛光造成的。
多年前,大多数精抛光都是通过用木棒和毛毡手工研磨来进行取的。对钢材施加过度应力的危险可以忽略不计。今天,没有一家商家负担得起手工抛光所需的时间,因此我们必须进行机械抛光。但是使用抛光机时,因为很容易施加压力和过快速度对钢表面产生应力。
当抛光员遇到橘皮或者一些麻点问题时,第一反应之一就是责怪钢材也加强对劣质钢材的怀疑。因此,钢铁企业对此进行了大量研究。根据一些研究结果和各种模具钢的实际经验,汇总了以下有关橘皮形成原因的信息。
几乎你对一块钢所做的任何工作都会强调它。传统的加工会给它带来很大的压力。 EDM 燃烧会给它带来压力,磨削会给它带来压力。硬质合金和陶瓷加工会给它带来巨大的压力。在实际工作条件下,在您将其抛光之前,该块几乎从未消除压力,因此您开始时会遇到障碍。
每种模具钢的表面都有一定的屈服点。该表面在抛光工具下像塑料一样的移动。如果您不将其移出其屈服点,它将返回其原始位置。如果您对它施加超过屈服点的压力,钢将保持在该位置,并且您在表面上产生了相当于很小的波纹。如果您继续加工钢材,您会将撕掉这些波纹的顶部并产生凹坑。即使您在完成抛光时没有看到凹坑,它们也可能在模具运行时出现,因为那里涉及应力,并且它们肯定会在生产后的重新抛光中出现。当然,如果橘皮不是太严重,点蚀可能不会出现。
在实际生产中,几乎不可能对模具进行机械抛光而完全没有一些橘皮。请记得,当您匆忙并开始对抛光工具施加过大的压力和过快的速度时,情况会变得更糟。抛光时您会注意到,抛光的钢材越硬,橘皮的可能性就越小。钢材越硬,屈服点就越高,并且在出现波纹和撕裂之前需要更大的抛光压力。
洛氏硬度在 30 多的模具钢不会能和洛氏硬度在 50 的模具钢那样抛光。在抛光软钢时,必须密切注意刷子和毛毡,以确保持在较低的保速度和压力。抛光员还必须密切注意保持抛光机台的旋转速度并尽快进入下一步,以便将旋转交通保持在最低限度。
当不锈材料开始在模具行业越来越受欢迎时,钢铁公司对抛光过程中的钢点蚀有很多抱怨。客户观点是劣质钢材。结果证明这一般都是因过度抛光而引起的。不锈钢对抛光压力非常敏感,表面容易移动和凹坑。不过如果小心处理,两者都会快速达到亮面。
造成橘子皮的另一个原因
造成橘皮的另一个原因是在热处理过程中过热。坩埚钢公司发布的信息表明,在热处理中过热的钢将在其结构中保留一些奥氏体,而不是将其全部转化为马氏体。奥氏体比马氏体更软,所以你有一个表面有坚硬和柔软的区域产生波纹或橘皮。
作为一名抛光技术员,无论你在抛光时多么小心,偶尔也会遇到一块钢材料在磨石块中看到钢材质剥落。磨石下的柔软区域磨损得更快,波浪纹路开始显露出来。你可再用手工加工修复,但效果还是不好。
橘子皮怎么办
您可以采取一些措施来尝试纠正这种情况。您可以返回到 600 油石从磨修复橘皮部分且真正深入去除其波浪表面。要更加注意手功研磨压力、速度和交义打磨方式均匀研磨表面也确保没有坑点。也应确定此钢材以作应力释放处理。低于钢的回火温度。应该在大约 100oF 下完成使块体退火。
然后用 600 砂砾磨石重新打磨模块,用 600 砂砾水性砂纸去除这些线条,之后如之前步骤用金刚石膏抛光,这次要更加小心,保持在最低的抛光压力。不要跳过任何步骤,并且小心不要在每一个步骤中花费超过必要的时间,从而减少抛光时对模块的整体应力。
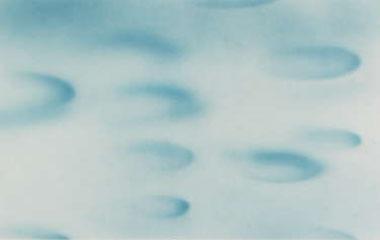
“橘子皮”
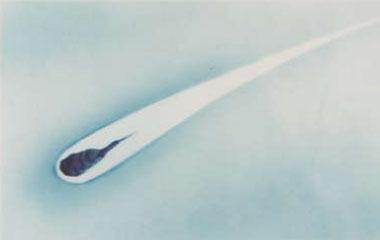
从表面去除微小颗粒,导致空洞和出现类似“彗星尾巴”
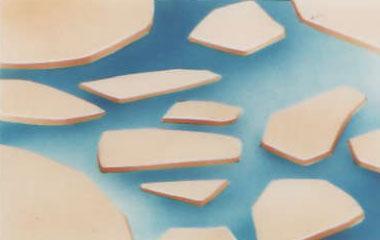
金属之间的不均匀平整度有时称为“浮雕”
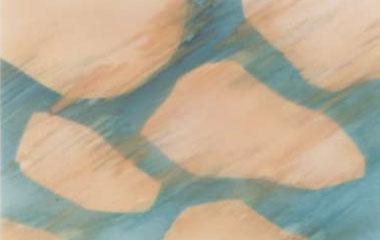
金属的表面流动或涂抹导致金属之间边界模糊
表面处理图表
Rt (μm) | Rz (μm) | CLA Ra (μm) | CLA Ra (μ”) | RMS | RMS |
---|---|---|---|---|---|
(μm) | (μ”) | ||||
0.06 | 0.03 | 0.006 | 0.2 | 0.007 | 0.2 |
0.08 | 0.04 | 0.008 | 0.3 | 0.009 | 0.3 |
0.1 | 0.05 | 0.01 | 0.4 | 0.011 | 0.4 |
0.12 | 0.06 | 0.012 | 0.5 | 0.013 | 0.5 |
0.15 | 0.08 | 0.015 | 0.6 | 0.018 | 0.7 |
0.2 | 0.1 | 0.02 | 0.8 | 0.022 | 0.9 |
0.25 | 0.12 | 0.025 | 1 | 0.027 | 1.1 |
0.3 | 0.15 | 0.03 | 1.2 | 0.033 | 1.3 |
0.4 | 0.2 | 0.04 | 1.6 | 0.044 | 1.8 |
0.5 | 0.25 | 0.05 | 2 | 0.055 | 2.2 |
0.6 | 0.3 | 0.06 | 2.4 | 0.066 | 2.6 |
0.8 | 0.4 | 0.08 | 3.2 | 0.088 | 3.5 |
0.9 | 0.5 | 0.1 | 4 | 0.11 | 4.4 |
1 | 0.6 | 0.12 | 4.8 | 0.13 | 5.2 |
1.2 | 0.8 | 0.15 | 6 | 0.18 | 7.2 |
1.6 | 1 | 0.2 | 8 | 0.22 | 8.8 |
2 | 1.2 | 0.25 | 10 | 0.27 | 10.8 |
2.5 | 1.6 | 0.3 | 12 | 0.33 | 13.2 |
3 | 2 | 0.4 | 16 | 0.44 | 17.6 |
4 | 2.5 | 0.5 | 20 | 0.55 | 22 |
5 | 3 | 0.6 | 24 | 0.66 | 26 |
10 | 6 | 1.2 | 48 | 1.3 | 52 |
15 | 10 | 2.5 | 100 | 2.7 | 108 |
30 | 20 | 5 | 200 | 5.5 | 220 |
50 | 40 | 10 | 400 | 11 | 440 |
100 | 80 | 20 | 800 | 22 | 880 |
200 | 160 | 40 | 1600 | 44 | 1760 |
400 | 320 | 80 | 3200 | 88 | 3500 |
注:等效值只是一个近似值。根据表面光洁度的特性,误差可能约为25%